أبرز 9 طرق لتحسين كفاءة التصنيع والإنتاج بالمؤسسات
8 دقائق للقراءة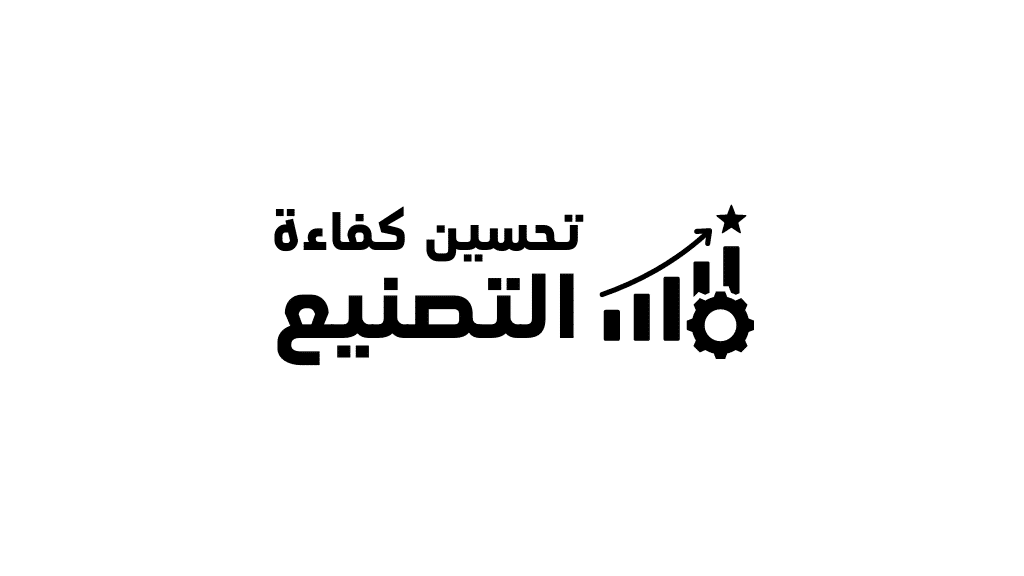
استثمار المؤسسة في تحسين كفاءة التصنيع والإنتاج يعد من أهم الخطوات في طريق البقاء في الصدارة، فكيف يمكن للمؤسسات تحقيق ذلك؟ وما أبرز التحديات التي تعيق التحسين؟
هذا ما نتعرف عليه بالتفصيل من خلال المقال.
أهمية تحسين الكفاءة في عمليات التصنيع والإنتاج
تلعب خطوة تحسين كفاءة التصنيع دورًا فعالًا في تطور المؤسسة، فمن خلالها ستتمكن من:
تقليل التكاليف
يساعد تحسين الكفاءة في التصنيع والإنتاج على تقليل التكاليف التشغيلية من خلال القضاء على الهدر، وتحسين استخدام الموارد، وتبسيط العمليات، مما يزيد الربحية، ويضمن تحديد الأسعار بشكل تنافسي.
زيادة الإنتاجية
تعمل خطوة تحسين الكفاءة على تعزيز الإنتاجية من خلال تقليل أوقات التوقف، وتحقيق أقصى استفادة من أنظمة التصنيع.
وذلك يسمح للشركات بتلبية متطلبات العملاء بشكل أكثر فاعلية، إنتاج وتسليم المزيد من المنتجات للعملاء في وقت أقل، مما يزيد من كفاءتها، وقدرتها على تحقيق المزيد من الأرباح.
تحسين الجودة
تضمن عمليات التصنيع الفعالة درجة عالية من الدقة، مما يحسن الجودة، ويقلل عيوب الصناعة والأخطاء، مما يمكنك من الحفاظ على رضا العملاء وسمعة العلامة التجارية، ويخلصك من الحاجة إلى إعادة العمل.
خلق ميزة تنافسية
تحقيق مستويات عالية من كفاءة التصنيع والإنتاج يمنح الشركات ميزة تنافسية كبيرة، إذ يتيح لهم تقديم أسعار أفضل، وتوصيل المنتجات بشكل أسرع، والحفاظ على مستوى متفوق من الجودة، مما يضعهم في موقع قيادي في الصناعة.
أبرز طرق تحسين كفاءة التصنيع والإنتاج
السعي نحو التحسين يعد أولى خطوات الحفاظ على النجاح، ومن أهم الطرق التي يمكن اتباعها:
1- تنفيذ منهجيات التحسين
هناك بعض المنهجيات التي يمكنك تنفيذها بهدف تحسين الكفاءة بالمؤسسة، ومن أبرزها:
منهجية كايزن – Kaizen
كايزن هو مصطلح ياباني يعني “التغيير نحو الأفضل”، وتقوم تلك المنهجية على:
- التوجيه، والحث على التطوير بدلاً من إلقاء اللوم على الأفراد عند حدوث مشكلات.
- التحسين المستمر، إذ تؤكد منهجية كايزن على أن التحسين هو عملية مستمرة لا تنتهي أبدًا.
- مشاركة الجميع في تحديد وتنفيذ أفكار التحسين على جميع مستويات المنظمة.
- التشجيع على التحسينات الصغيرة والمستمرة، إذ تكون لها فوائد كبيرة على المدى الطويل.
- القضاء على الهدر بجميع أشكاله، بما في ذلك الوقت والموارد والمواد.
- وضع واتباع إجراءات التشغيل القياسية للحفاظ على التسلسل والجودة.
وبالتالي تعد منهجية كايزن جزءًا أساسيًا من استراتيجية تحسين كفاءة التصنيع والإنتاج، وتعزيز الوعي بالجودة والكفاءة.
منهجية 6 سيجما
منهجية مبنية على تحليل البيانات، بهدف تقليل الأخطاء، والتباين في العمليات، وذلك من خلال عدة مبادئ رئيسة يتم اختصارها في (DMAIC)، وهي:
تعريف – Define
في تلك الخطوة يتم تحديد المشكلة أو فرصة التحسين بوضوح، ووضع أهداف ملائمة للأهداف الاستراتيجية العامة للمؤسسة.
قياس – Measure
هنا يتعين على أصحاب الشأن تحديد معايير للقياس، ووضع خطة لجمع البيانات، واستخدم التحليل الإحصائي لفهم الأداء الحالي للعملية، وتقييم حجم المشكلة.
تحليل – Analyze
تقوم تلك الخطوة على تحليل البيانات التي تم جمعها لتحديد الأسباب الجذرية للمشكلة، واستخدم الأدوات للتحقق من صحة تلك الأسباب.
تحسين – Improve
الخطوة الرابعة في منهجية 6 سيجما هي تقييم الحلول المقترحة أو أفكار التحسين، وإجراء اختبارات تجريبية للتحقق من فعالية التحسينات.
تحكم – Control
تحتاج المؤسسة في تلك الخطوة إلى:
- وضع خطط رقابة، لضمان استدامة التحسينات بمرور الوقت.
- تنفيذ آليات المراقبة والتحكم لتتبع أداء العمليات.
- توفير التدريب، لضمان نتائج متسقة وموثوقة.
- تحديد إجراءات التشغيل القياسية.
بعد ذلك تركز المنهجية على الاعتراف والاحتفاء بإنجازات وجهود أعضاء الفريق المشاركين في مشروع التحسين.
ومن ثم يتضح أن تلك المبادئ تمثل نهجًا منظمًا لتحسين كفاءة التصنيع والإنتاج، وتحقيق التميز التشغيلي.
2- إجراء مراجعات دورية للعمليات
تشمل هذه المراجعات تقييم العمليات بناءً على معايير الجودة والكفاءة، لمعرفة المجالات التي تحتاج إلى تحسين، وتحديد الأخطاء والعوائق والتكاليف الزائدة، مما يسمح للشركة بتحديد الإجراءات اللازمة لتحقيق التحسين المستمر.
لو طبقنا تلك الخطوة على مثال صناعة السيارات نجد أنه في عملية التصنيع، يمكن تنفيذ فحص دوري لمختلف مراحل الإنتاج بما في ذلك:
- تجميع المحرك
- التثبيت الكهربائي
- تشكيل الهيكل
- الطلاء
- التجهيز النهائي
أما أثناء الفحص، فيتم تحديد أية مشكلات محتملة مثل: عدم اتباع المعايير، وتكرار الأخطاء، وتأخر الإنتاج، ونقص في جودة المنتجات. إلى جانب استعراض استخدام الموارد مثل: العمالة، والمعدات، والمواد الخام، وتحديد فرص لتحسين استخدامها.
من خلال توثيق الملاحظات يمكن تطبيق تحسينات في العمليات التصنيعية. على سبيل المثال، إذا اكتشفنا أن هناك تأخيرًا في عملية التجهيز النهائي بسبب عدم تنظيم الخطوات، فيمكن التفكير في كيفية تحسين التخطيط، وتنظيم العمل.
3- تشجيع اقتراحات الموظفين ومشاركاتهم
تشجيع الموظفين على تقديم الاقتراحات والمشاركة في تحسين كفاءة التصنيع والإنتاج يخلق ثقافة عمل إيجابية تعزز الابتكار، والتحسين المستمر، فعندما يشعر موظفيك بأنهم جزءًا من العملية وأن آرائهم تهم، فإنهم يكونون أكثر استعدادًا لتقديم اقتراحات تساهم في تحسين الأداء.
إليك بعض الأمثلة التي يمكنك تنفيذها لتعزيز المشاركة واقتراح الآراء:
عقد جلسات العصف الذهني (Brainstorming)
يمكن تنظيم جلسات العصف الذهني، لطرح الأفكار، والتحديات المتعلقة بالتصنيع والإنتاج، إذ تحفزهم هذه الجلسات على تبادل الأفكار والخبرات، وتقديم اقتراحات جديدة.
على سبيل المثال، يمكن أن تشمل تلك الجلسات تقييم الوضع الحالي، وتحديد العقبات، وتطوير خطط للتحسين.
إنشاء بوابة لإرسال الاقتراحات
إن إنشاء وسيلة سهلة ومباشرة لاستقبال اقتراحات الموظفين يشجعهم على تقديم أفكارهم، لثقتهم في في أن أفكارهم ستصل إلى الجهات المعنية وسيُنظر فيها بعناية، ويمكنك اعتماد البريد الإلكتروني أو منصات التواصل الداخلي كبوابة لتلقي الاقتراحات.
تصميم برامج للتكريم والمكافآت
يمكنك اختيار أفضل الاقتراحات، وتكريم الموظفين الذين قدموها من خلال توزيع شهادات أو منح مكافآت مالية أو ترقيات، إذ يشجعهم ذلك على المشاركة المستمرة في عملية تحسين كفاءة التصنيع والإنتاج، وتقديم المساهمات القيمة.
4- إنشاء وقياس مؤشرات الأداء الرئيسية – KPIs
تعد مؤشرات الأداء (KPIs) أدوات هامة لتقييم تحقيق الأهداف، لذا يجب على المنشآت تحديد وتعريف المؤشرات الأساسية التي تتوافق مع أهداف الإنتاج والتصنيع.
يمكن أن تشمل المؤشرات الرئيسية العديد من المجالات مثل:
- الكفاءة في استخدام الموارد
- الجودة
- الإنتاجية
- مستويات الخدمة
- التكاليف
- مدة التسليم
لا تغفل عن مقارنة عملك بمعايير الصناعة، وأفضل الممارسات، إذ يعد ذلك من أبرز الأدوات الفعالة لتحسين الكفاءة في التصنيع والإنتاج.
5- ضبط الجودة والاستثمار في أنظمة فعالة لإدارتها
تعد عمليات ضبط الجودة الدقيقة أحد العناصر الأساسية لتحسين كفاءة التصنيع والإنتاج. يشير ضبط الجودة إلى تطبيق مجموعة من الإجراءات والمعايير للتأكد من تلبية المنتجات لأعلى معايير الجودة.
يتضمن ذلك تنفيذ إجراءات منتظمة، للتأكد من توافق المنتج مع المواصفات المحددة ومتطلبات العملاء.
أما عن أنظمة إدارة الجودة فهي أدوات قوية لتحسين الكفاءة في التصنيع، إذ تهدف إلى تطبيق إجراءات متكاملة، لضمان الجودة والتحسين المستمر، ويعتمد نجاحها على التزام المؤسسة بمعايير الجودة وتطبيق الممارسات الأفضل.
وخلاصة القول هنا أنه من خلال تنفيذ عمليات ضبط الجودة الدقيقة، وإجراء تدقيقات دورية والاستثمار في أنظمة إدارة الجودة، يمكن للمنشأة تحقيق تحسين في جودة المنتجات، وتقليل العيوب، وزيادة الكفاءة، وتحقيق رضا العملاء، وتعزيز قدرتها على المنافسة في سوق التصنيع والإنتاج.
6- التعاون الوثيق مع الموردين والبائعين
التعاون الوثيق مع الموردين والبائعين هو عنصر حاسم في تحسين كفاءة التصنيع والإنتاج، إذ يٌمكن المؤسسات من:
مشاركة المعلومات والتخطيط المشترك
من خلال التواصل المستمر مع الموردين والبائعين، يتم تبادل المعلومات حول الاحتياجات التصنيعية والمواصفات والجداول الزمنية، وبالتالي يمكن لهذا التعاون تحسين توقيت التسليم، وتخفيض تكاليف الشحن، وتحسين التنسيق العام للتصنيع.
تطوير المنتجات والمواد
يمكن للمؤسسة الاستفادة من خبرة وتوجيهات الشركاء في تطوير المنتجات واختيار المواد المناسبة، مما يحسن الجودة، ويقلل التكاليف من خلال استخدام مواد أكثر كفاءة واقتصادية.
تحسين سلاسل التوريد
يساعد التعاون الوثيق مع الموردين على تحسين سلاسل التوريد وتقليل التكاليف اللوجستية، فعلى سبيل المثال، يمكن للتعاون في تخطيط الإنتاج والتوزيع أن يقلل التخزين الزائد، ويوفر تكاليف النقل والتخزين.
التفاوض على الشروط التجارية
يتيح التعاون مع الموردين والبائعين فرصة للتفاوض على الشروط التجارية بشكل أفضل مثل: الأسعار، وشروط الدفع، وسياسات الإمداد والتسليم، مما يحقق توفير ملحوظ في التكاليف.
7- تنفيذ تصنيع بالتوقيت الزمني المناسب (JIT)
تركز تلك المنهجية في التصنيع على تقليل المخزون، وتحسين كفاءة التصنيع، لتسليم المنتجات في الوقت المناسب دون وجود تراكمات زائدة أو نقص في المخزون.
عند تنفيذ JIT، تشتري المؤسسة المواد الخام وتوردها إلى خط الإنتاج عند الحاجة الفعلية لها فقط بدلاً من الاعتماد على المخزون الكبير، ويتم توريد المواد بكميات دقيقة وفقًا لجدول الإنتاج والطلب الفعلي، مما يقلل من التكاليف المترتبة على تخزين المواد.
علاوة على ذلك، تنظم المؤسسة عمليات التصنيع والإنتاج بشكل دقيق وفقًا للإنتاجية الفعلية والطلب من العملاء، وتضبط جدول الإنتاج، لتحقيق توازن بين معدل الإنتاج والطلب.
على سبيل المثال، لنفترض أن شركة لتصنيع السيارات تعتمد على نظام JIT، فعند استلام طلب من العملاء لشراء سيارة معينة، يتم:
- إنشاء طلبية للمواد اللازمة لتصنيع السيارة بناءً على المواصفات المطلوبة.
- توريد المواد الخام إلى خط الإنتاج بالتوازي مع تقدم العملية الإنتاجية.
وبالتالي يضمن ذلك توفر المواد في الوقت المناسب لكل مرحلة من مراحل التصنيع، ويسمح بالانتقال السلس بين المراحل، وتقليل فترات الانتظار غير الضرورية، وتحسين تدفق العمل، وتلبية متطلبات العملاء بدقة في الوقت المحدد.
8- التدريب المستمر وتطوير المهارات
التدريب المستمر للموظفين يعد عنصرًا أساسيًا في تحسين كفاءة التصنيع والإنتاج، إذ يمكنهم من:
- التكيف مع التقنيات والعمليات الجديدة.
- زيادة فهم طبيعة التصنيع والإنتاج.
- تحسين كفاءتهم وإنتاجيتهم.
يمكن تنفيذ التدريب المستمر عن طريق توفير ورش عمل ودورات تدريبية للموظفين تشمل التعريف بتقنيات الإنتاج الجديدة، وأدوات التحسين المستمر، وتحليل البيانات، وإدارة الجودة الشاملة.
يمكن أيضًا توفير دورات تدريبية خارجية للموظفين للحصول على المعرفة الأكثر تحديثًا في مجالاتهم المهنية، حتى تكون لديهم الخبرة الكافية لتحسين كفاءة التصنيع والإنتاج بالمؤسسة.
9- استخدام نظام ERP
يعد نظام ERP أحد الأدوات الرئيسية التي تساهم في تحسين الكفاءة في التصنيع والإنتاج، إذ يهدف النظام إلى تكامل الأقسام داخل المنشأة في نظام مركزي متكامل، مما يساهم في:
توفير الوقت والجهد
يسهل نظام ERP الوصول إلى المعلومات اللحظية من أي مكان وفي أي وقت، ويقلل من الجهد المبذول في إدخال البيانات بشكل متكرر، فعلى سبيل المثال، يمكن للموظفين إدخال البيانات مرة واحدة في النظام ومشاركتها بسهولة مع الأقسام الأخرى.
تحسين الاتصال والتنسيق
بفضل نظام ERP يتسنى للأقسام المختلفة التواصل والتنسيق بشكل أفضل، فمثلًا يمكن لقسم الإنتاج أن يطلع على حاجة قسم المبيعات للمنتجات، ويخطط وفقًا لها، مما يقلل من المخزون الزائد، ويحسن استجابة المؤسسة لطلبات العملاء، ويقلل من تكلفة نفاد المخزون.
مراقبة تحليل البيانات
يوفر نظام ERP ميزة تتبع البيانات وتحليلها بشكل متقدم، مما يتيح تكوين رؤية شاملة لسير العمليات، فمثلًا تستطيع الإدارة الاطلاع على تقارير التكاليف، والكفاءة، والإنتاجية والجودة، وبناء على هذه البيانات يمكن اتخاذ قرارات استراتيجية لتحسين كفاءة التصنيع والإنتاج.
وبالتالي فلا غنى عن وجود نظام ERP فعال في مؤسستك، وأفضل خيار لك هو “إدارة“,
تعرف أكثر على تفاصيل “إدارة” من خلال مقال: 9 خدمات أساسية يقدمها “إدارة”.
تحديات تحسين الكفاءة وكيفية التغلب عليها
الطريق إلى التحسين ليس ممهدًا بشكل كامل، فهناك بعض التحديات التي تواجه أصحاب الأعمال عند اتخاذ قرارات التطوير، ومن أبرزها نجد:
1- مقاومة التغيير
يمكن أن يواجه المشروع تحديًا من الموظفين الذين يعارضون التغيير، ويرفضون التعاون في تحسين الكفاءة، فقد تكون لديهم مخاوف من فقدان الوظائف أو التغيير في طبيعة العمل.
وللتغلب على ذلك ينبغي على الشركات اتباع الإجراءات التالية:
- التواصل بشكل واضح حول الأهداف والفوائد المترتبة على تحسين الكفاءة.
- توفير التدريب المناسب، وفرص التطوير للموظفين، لتعزيز مهاراتهم.
- تشجع على المشاركة المباشرة للموظفين في عملية تحسين كفاءة التصنيع.
2- ارتفاع تكاليف الاستثمار الأولية لاعتماد الأنظمة الحديثة
يشكل التحول إلى تقنيات جديدة ومعدات متطورة تكلفة استثمارية عالية في البداية، ويمكن أن يكون هذا تحديًا خاصة للشركات الصغيرة والمتوسطة، لذا لا بد من:
- تقييم تكلفة الاستثمار الجديدة بعناية، وتحليل العائد المتوقع على الاستثمار.
- البحث عن شركاء يمكنهم تقديم حلول مالية للمساعدة في تغطية تكاليف الاستثمار الأولية.
- التفكير في خطة تطبيق الآليات الجديدة بشكل تدريجي بدلاً من تطبيقها بشكل كامل وفوري.
3- تحقيق التوازن بين الاهتمام بالعوامل الداخلية ومتطلبات العميل
يتعين على الشركات إيجاد توازن بين تحقيق الكفاءة في عمليات التصنيع والإنتاج وبين القدرة على التكيف مع متطلبات العملاء، وللتغلب على ذلك يمكن:
- استخدام تقنيات التصنيع المرنة التي تتيح تعديل العمليات بسهولة، والتكيف مع تغيرات الطلب وتفضيلات العملاء.
- تحسين التخطيط والتنسيق بين الإنتاج والمبيعات والتوريد لضمان تحسين كفاءة التصنيع.
- الاعتماد على الابتكار المستمر والبحث والتطوير لتحسين العمليات، وتطوير منتجات جديدة تلبي متطلبات العملاء المتغيرة.
الخلاصة
يتطلب تحسين كفاءة التصنيع والإنتاج في المؤسسات اعتماد استراتيجيات فعالة ومتكاملة مثل تطبيق منهجية كايزن و 6 سيجما، وإجراء المراجعات الدورية، وتشجيع الاقتراحات، لاكتشاف فرص جديدة للتحسين.
وتسهيلًا لتطبيق هذا التحسين احرص على توفير نظام ERP متكامل يساعدك على الربط بين جميع الأقسام والفروع في نظام مركزي واحد، لتتمكن من تحليل البيانات، واتخاذ القرارات الفعالة نحو التطوير.
تواصل معنا واطلب عرضًا توضيحيًا.
المراجع
مقالات ذات صلة
دليلك الشامل لمعرفة كل ما يتعلق بـ”إدارة المخزون”1
إدارة المخزون هو الأساس لكل تجارة، ففشلك في إيصال المنتجات للمستهلك سيتسبب في خسارتك للأموال والعملاء على حد سواء. التخطيط السليم لطلب البضاعة من المكان الصحيح، في الوقت المناسب وبالكمية…
10 أدوات يحتاجها عملك في التجارة الإلكترونية
إنجاز الأعمال بكفاءة أعلى وفي وقتٍ أقل هو الاتجاه الذي يسلكه أصحاب المؤسسات مؤخرًا، كما أنه أصبح حاجة ضرورية في ظل التحديات المعاصرة كأزمة كورونا التي أنتجت ضرورة العمل عن…
أهمية نظام الحوافز في الشركات وكيفية إدارته بفاعلية من خلال “إدارة”
زيادة في الإيرادات بنسبة أكبر من 40%! هذا ما يحدث عند تطبيق نظام الحوافز في الشركات لمكافأة الموظفين تبعًا للدراسة التي أجرتها Harvard Business Review، وبالتالي ففهم آلية تنفيذ هذا…